


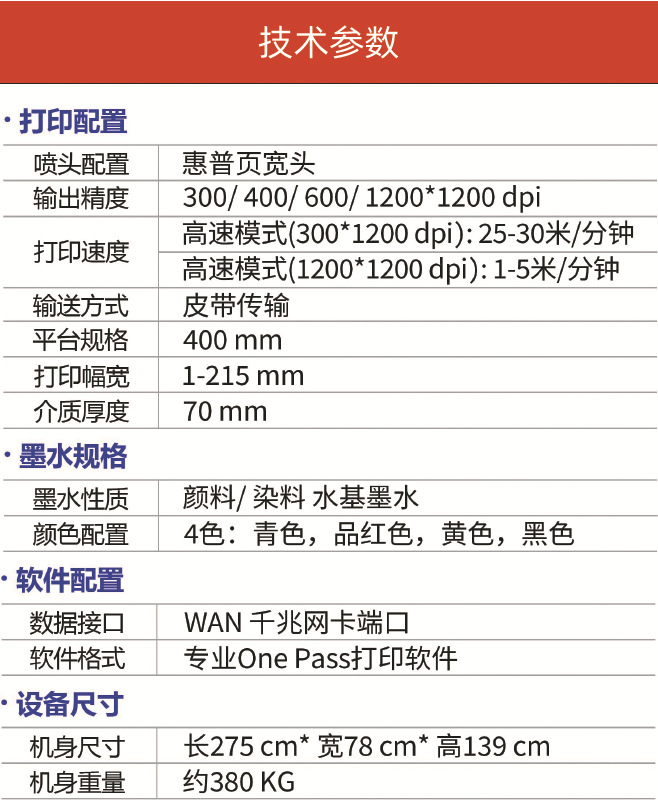


不干膠標(biāo)簽又叫自粘標(biāo)簽材料以紙張、薄膜或其它特種材料為面料,背面涂有膠粘劑,以涂硅守護(hù)紙為底紙的一種復(fù)合材料。并經(jīng)印刷、模切等加工后作為成品標(biāo)簽。

不干膠材料一般在標(biāo)簽聯(lián)動機上印刷與加工,最平常的印刷形式為凸印,其它印刷方式亦有應(yīng)用。
01印刷周期平常故障
故障1:印刷后的標(biāo)簽表面墨層不干,干燥慢或墨層一擦就掉
原由:印刷墨層太厚,墨量太大以及油墨中所運用的添加劑不合適、油墨變性或運用的油墨種類不合適等都會導(dǎo)致印刷后的標(biāo)簽?zāi)珜硬桓?、干燥慢或墨層一擦就掉?span style="color: green;">另外,設(shè)備運轉(zhuǎn)速度太快、干燥……
處理辦法
1、采用深墨薄印的辦法來減少墨層的厚度;
2、運用干燥快的專用油墨;
3、運用配套的添加劉,加放配套的干燥劑;
4、采取辦法,延長印刷品的干燥或固化時間;
5、加強室溫,適量排風(fēng),加快油墨干燥速度。
故障2:薄膜表面印刷墨層附著牢度差,易掉墨
原由:薄膜表面未經(jīng)電暈處理,或薄膜的表面張力小于油墨的表面張力,引起油墨很難附著;沒運用的油墨與薄膜材料特性不匹配或運用的不是專用油墨時,亦會產(chǎn)生此類故障;而運用過期或失效油墨亦不可避免地顯現(xiàn)此類故障。另一,烘干安裝(UV或紅外熱風(fēng)干燥)功率低,致使油墨不可完全干燥或印刷墨層太厚、墨量太大、油墨粘度太大致使長期烘干后油墨脆化,亦將引起薄膜表面印刷墨層附著牢差差,易掉墨。
處理辦法
1、加強承印材料的表面張力,需求表面張力值要達(dá)到38達(dá)因/厘米以上;
2、輪轉(zhuǎn)標(biāo)簽機應(yīng)安裝電暈安裝,經(jīng)過隨機電暈算是業(yè)加強薄膜的表面張力;
3、可先用透明的溶劑型油墨進(jìn)行預(yù)訂打底來加強承印材料的表面張力;
4、選擇與承印材料匹配的專用油墨和配套添加劑;
5、加強烘干或固化功率,或降低設(shè)備運行速度,增多烘干時間;
6、印刷墨層要盡可能薄,墨量要盡可能少,必要時可單色多次疊??;
7、舉薦印刷后進(jìn)行UV上光,以守護(hù)印刷墨層,增多墨層的附著牢度。
故障3:印在FASCLEAR和PRIMAX上的油墨附著牢度差
原由:FASCLEAR和PRIMAX材料均為柔軟的亞光表面,表面強度差,用指甲輕劃即會顯現(xiàn)劃痕,無論其表面張力是高是低,都會顯現(xiàn)油墨附著牢度差的問題,況且,即使是在其它承印材料上不會顯現(xiàn)附著牢度問題的油墨,印在FASCLEAR和PRIMAX材料上亦會顯現(xiàn)油墨附著牢度差的問題。此處的所說掉墨,實質(zhì)上是承印材料的表面被損壞了,與油墨基本無關(guān)。
處理辦法
在油墨和上光油中加放硬化劑,或購買加有硬化劑的油墨,經(jīng)過增多油墨和上光油的耐摩擦強度與硬度來達(dá)到改善油墨在FASCLEAR和PRIMAX材料上的附著牢度的目的。
故障4:卷筒易碎紙端面滲膠后,沒法開卷印刷
原由:分切復(fù)卷小卷時復(fù)卷張力太大,引起復(fù)卷太緊,會誘發(fā)此故障;倉儲或印刷車間溫度太高亦會引起此故障;而遭受擠壓或倉儲時間過長亦是引起此故障的原由之一。
處理辦法
1、除針對以上原由改善相應(yīng)的倉儲和加工要求外,還可用酒精擦抹滲膠端面,使粘合劑稀釋,降低其粘度,以利于開卷;
2、輕輕開卷,兩端上粉并重新緩慢復(fù)卷;
3、改善后的卷筒不干膠材料在間歇式輸紙的標(biāo)簽機上要慢速印刷和模切
故障5:印刷后的薄膜表面局部掉墨——油墨附著牢度不一致
原由:其一多色疊印時,底層油墨尚未完全干燥即被表面油墨所遮蓋;其二,因為墨層過厚,導(dǎo)致暴露在外的同色油墨已完全干燥,而壓在底下的油墨仍得不到干燥;其三,單色組的UV固化功能。
處理辦法
1、減薄墨層的厚度;
2、增多VU干燥安裝的固化功率;
3、降低設(shè)備速度,增多油墨固化時間,可采用單色多工位固化;
4、在工藝設(shè)計上要盡可能避免墨層疊印,可采用圖形邊緣漲色并列印刷的工藝;
5、增大電暈處理安裝的功率,加強承印材料的表面張力,使油墨更易干附著,從而增多油墨的附著牢度;
6、運用固化速度快的油墨或在油墨中增多光敏劑(干燥劑)。

故障6:實地印刷墨層表面魚眼
原由:魚眼是由于紙毛,紙屑或灰塵導(dǎo)致的。顯現(xiàn)魚眼既與環(huán)境的清潔程度和車間密封狀況相關(guān),亦與靜電相關(guān),由于靜電會將灰塵和紙屑等雜質(zhì)吸附到承印材料表面;顯現(xiàn)魚眼還與承印材料本身的質(zhì)量有磁,密度不均勻,涂層牢靠度低,纖維短且牢靠度低的承印材料就容易顯現(xiàn)魚眼問題;另一,分切質(zhì)量欠好,分切精度低的承印材料亦易顯現(xiàn)魚眼問題。
處理辦法
1、改善、凈化生產(chǎn)環(huán)境,有要求的印刷廠家應(yīng)對印刷機進(jìn)行密封管理;
2、在印刷機上安裝靜電消除器和承印材料清潔器,以防止灰塵和紙屑遺留在承印材料表面;
3、選擇高質(zhì)量的承印材料,要求其表面涂層要有較強的牢靠度,很難膠落;
4、加強卷筒材料的分切質(zhì)量,防止材料端面或周邊產(chǎn)生碎屑;
5、定時清洗印版和印刷機的輸墨系統(tǒng)。
故障7:紙張類材料掉粉
原由:紙張自己質(zhì)量差,表面涂層牢靠度低就容易掉粉;環(huán)境潮濕或材料本身的問題使承印材料涂層表面強度降低或油墨粘度太大亦容易導(dǎo)致掉粉故障;另一,掉粉還同標(biāo)簽的壓機方相關(guān)。
處理辦法
1、選擇優(yōu)秀承印材料,尤其是大面積實地印刷時;
2、降低油墨粘度,需求各色序所用的印刷油墨的粘度要依次遞減;
3、改善材料的儲存環(huán)境和印刷環(huán)境,降低環(huán)境濕度;
4、在工藝設(shè)計上變實地印刷為平網(wǎng)印刷;
5、正式印刷前先走空紙進(jìn)行預(yù)印,能夠去掉部浮粉;
6、改換印刷設(shè)備壓印方式,減少印刷接觸面積。
故障8:單印印刷套印不準(zhǔn)
原由(1):紙張尺寸不穩(wěn)定導(dǎo)致的套印不準(zhǔn)。因為紙張所處的印刷加工環(huán)境同復(fù)合制造時環(huán)境濕度區(qū)別導(dǎo)致紙張尺寸變化;紙張表面水分含量不均勻,導(dǎo)致紙張四邊變形或局部變形;同一規(guī)格尺寸的紙張中,因為部分紙張的纖維方向不一致,導(dǎo)致其收縮率區(qū)別;而車間的溫度、濕度不穩(wěn)定則會導(dǎo)致很強幅度的紙張尺寸變化。
處理辦法
1、將印刷車間漸度掌控在20—22攝氏度,相對濕度掌控在50%。
2、將潤版液用的掌控在最低水平,以減少紙張的抽漲變形;
3、盡可能運用多色印刷機一次走紙完成多色印刷;
4、采用單色機多次印刷進(jìn)要守護(hù)好半成品,最好用塑料布密封,尤其是在雨季;
5、運用纖維方向一致的紙張,區(qū)別纖維方向的紙張要分別堆放,印刷;
6、在要求準(zhǔn)許的狀況下,紙張應(yīng)提前進(jìn)入印刷車間,使其有充分的時間與環(huán)境溫濕度取得平衡。
7、對濕度過大的紙張,可采用預(yù)先空印的辦法,加快其與環(huán)境在溫濕度上的平衡;
8、對需要進(jìn)行燙金和模切的小標(biāo)簽,應(yīng)先印刷,待其尺寸穩(wěn)定后,再對照實質(zhì)尺寸制作燙金版和模切版。
原由(2):其它原由導(dǎo)致的套印不準(zhǔn),例如
1、紙張滲膠,使前規(guī)、側(cè)規(guī)不到位,引起套印不準(zhǔn);
2、紙張裁切定位時因為出現(xiàn)紙張回彈,歪斜而導(dǎo)致同一紙垛中的紙張不對正;印刷時難以套準(zhǔn);
3、理紙折痕導(dǎo)致紙張變形過大,導(dǎo)致民套印不準(zhǔn);
4、由靜電吸附導(dǎo)致套印不準(zhǔn);
5、裝版時,因為各色版拉伸變形,松緊區(qū)別,導(dǎo)致套印不準(zhǔn);
6、各色組橡皮布包襯不一致,變形量不一致導(dǎo)致套印不準(zhǔn);
7、滾筒襯墊增減辦法不正確導(dǎo)致套印不準(zhǔn);
8、由輸紙公司和傳紙公司的原由導(dǎo)致套印不準(zhǔn)。
處理辦法
1、運用不滲膠、合格的不干膠材料,要用涂撒滑石粉或用膠帶粘的辦法來改善滲膠狀況;
2、加強裁紙精度,必要時可重新裁切,并要正確理紙,不可變形過大;
3、安裝靜電消除器掌控靜電,并安裝加濕器來掌控車間溫濕度;
4、經(jīng)過打樣,使上版,包襯、橡皮布松緊一致,以保準(zhǔn)套準(zhǔn);
5、全套機組更換橡皮布或包襯,使各色組的橡皮滾筒彈性變形一致;
6、加強印刷機精度,保準(zhǔn)正確傳紙、輸紙。
故障9:版面墨色不一致
原由:印版壓力不均勻或版面上著墨量不均勻。
處理辦法
1、調(diào)節(jié)壓力,重新墊版臺;
2、調(diào)節(jié)墨斗或輸墨系統(tǒng),使著墨輥給墨量一致。
故障10:線條或網(wǎng)點處糊版,變形
原由:墨量過大,著墨輥與印版之間的接觸壓力過大或印刷壓力太大是引起糊版、網(wǎng)點變形的重點原由。
處理辦法
1、適當(dāng)減少墨斗輥的輸墨量;
2、減輕著墨輥與印版間的接觸壓力;
3、降低印刷壓力或?qū)|版臺進(jìn)行局部調(diào)節(jié)。

故障11:印刷品蹭臟、污背、粘連
原由:油墨未完全干燥或墨量太大。
處理辦法
1、降低印刷速度;
2、調(diào)節(jié)油墨,加放相應(yīng)的助劑;
3、可上晾紙架分層堆放;
4、適當(dāng)減少上墨量。
02模切周期故障與排除
故障1:平壓平式模切中底紙被切穿
原由:底紙厚薄不勻;一起模切版上的標(biāo)簽數(shù)量太多,面積過大;模切版不平整,精度低;模切公司精度低導(dǎo)致模切不穩(wěn)定;模切襯墊板不平整或有凸出點;模切刀片選取不正確。
處理辦法
1、盡可能選 用較厚的底紙或用均勻度較好的材料作底紙;
2、加強模切版精度,必要時請專業(yè)廠家來制造;
3、運用平整度好的襯墊板,并定時檢測,清潔和更換料墊板;
4、可采用大面積印刷后先縱切而后再小面積模切的辦法;
5、運用高精度的專用不干膠模切刀片來制作模切版。
故障2:模切后排廢時,紙邊經(jīng)常斷裂,沒法正常開機
原由:模切版或墊板不平整,引起紙邊局部未切斷;設(shè)備速度太快或太慢,導(dǎo)致不干膠承印材料牽引張力不合適;排廢邊太窄,標(biāo)簽尺寸太大或太細(xì)長,很難排廢;標(biāo)簽與底紙間離型力太大,紙邊承受不了反拉力;標(biāo)簽外形特殊,擺列不恰當(dāng),排廢困難。
處理辦法
1、加強模切版精度,減小模切面積;
2、模切底板要平整,并定時更換;
3、正確調(diào)節(jié)排廢張緊力;
4、正確設(shè)置廢紙邊的尺寸,以加強其抗拉強度;
5、換用剝離力合適的不干膠標(biāo)簽材料;
6、按照標(biāo)簽外形恰當(dāng)排版,使其便于排廢。
故障3:排廢時簽同紙邊一同揭下
原由:模切壓力不均勻,導(dǎo)致模切深淺不一致,使部分紙邊未被切斷;模要版運用時間過長;刀片太鈍,引起面材被壓進(jìn)底紙但未被切斷;設(shè)備右速度不合適,太慢或太快,影響排廢;排廢紙邊太窄,斷裂時顯現(xiàn)掉標(biāo)現(xiàn)象;紙邊的排廢方向不合適,選擇的不五膠材料不合適;底紙和面紙間的離型力太?。粯?biāo)簽面積太小,擺列辦法不合適;生產(chǎn)車間的溫度過低,使粘合性能出現(xiàn)改變。
處理辦法
1、調(diào)節(jié)模切版,加強模切精度,可在版面粘貼海綿;
2、變換設(shè)備速度,調(diào)節(jié)紙邊的排廢角或更換排廢輥;
3、運用離型力合適的不干膠材料,并恰當(dāng)安排排廢邊寬度。
03上光周期故障與排除
故障:UV上光中的平常質(zhì)量問題有:
1、上光后,經(jīng)地一段時間,印刷品發(fā)黃、發(fā)紅,改變顏色;
2、印刷品表面不亮;起褶或顯現(xiàn)條痕;
3、上光面發(fā)粘,不但滑;
4、上光層不牢,掉墨,有氣泡,麻點等。
處理辦法
1、運用高質(zhì)量、有效期內(nèi)的上光油;
2、恰當(dāng)掌控上光油的量,既不可太少亦不可太多,要重視流平效果;
3、重視底墨的印刷質(zhì)量,需求把墨量印足、印實,并不要干透;
4、按照上光表面的實質(zhì)狀況正確調(diào)節(jié)上光油的粘度;
5、正確調(diào)節(jié)上光油的表面張力,使其少于油墨的表面張力,可添加表面張力低的溶劑或表面活性劑;
6、避免油墨層晶化,必要時可對其進(jìn)行表面處理;
7、調(diào)節(jié)好設(shè)備速度、上光油量、烘干能量之間的關(guān)系。
04覆膜周期故障與排除
故障1:圖案發(fā)虛,薄膜與印品粘合不良
原由:覆膜輥表面有缺陷,硬度太低,以及覆膜輥壓力不足,或覆膜輥與底輥不平行,都會導(dǎo)致此故障;而印刷墨層太厚或覆膜時膜層尚未干透,或機速太快亦是產(chǎn)生此故障的原由。
處理辦法
1、加大覆膜輥壓力;
2、調(diào)節(jié)兩輥間的平行度;
3、若是覆膜輥本身有問題,則更換覆膜輥;
4、 降低機速或改變油墨成份。
故障2:圖案表面有壓痕凹點
原由:覆膜輥表面不干凈或已然磨損
處理辦法
清潔或更換覆膜輥
故障3:印刷品表面有皺紋
原由:復(fù)合膜太松或底紙拉力過大,以及復(fù)合膜兩邊張力不一致均會引起此故障。
處理辦法
1、張緊復(fù)合薄膜;
2、降低底紙拉力;
3、改用合適的復(fù)合薄膜。
故障4:標(biāo)簽貼在瓶體上翹邊
原由:紙張?zhí)』驈?fù)合膜太緊都容易使印刷品發(fā)翹,而復(fù)合膜太薄或有質(zhì)量問題,引故障更加是難以避免。
處理辦法
1、避免對薄紙格膜;
2、復(fù)合膜張力地大時,要換用剝離力小的或有底紙的復(fù)合膜。
3、單張紙覆膜時,張力方向應(yīng)與標(biāo)簽彎方向垂直;
4、要掌控好覆膜張力、壓力、速度,以保證覆膜精度;
5、覆膜適合小幅面標(biāo)簽,平面粘貼,大幅面標(biāo)簽意見采用上光工藝
故障5:圖紋內(nèi)起泡,發(fā)白
原由:覆膜時印刷墨層尚未干透,墨層太厚,覆膜壓力不足,復(fù)合膜太松或厚薄不均勻均會引起此故障。
處理辦法
1、增大復(fù)合壓力;
2、更換復(fù)合膜或調(diào)節(jié)其張力。
05燙金周期故障與排除
故障1:燙印不上或燙印不牢
原由:燙印溫度地低,印版壓力過低,印刷墨層表面晶化或太光滑,墨層太厚以及電化鋁型號不合適都有可能引起此故障。
處理辦法
1、適當(dāng)加強燙印溫度;
2、加大印版壓力;
3、改變油墨成份,使墨層表改性;
4、降低墨層厚度,減少疊??;
5、變換其它型號的電化鋁。
故障2:電化鋁反拉帶墨
原由:印刷墨層干燥不充分,油墨附著力太低以及電化鋁分離力過大都是引起此故障的原由。
處理辦法
1、燙印電化鋁之前,要讓油墨充分干燥;
2、改變油墨成份;
3、改用分離力低的電化鋁。
故障3:印跡滋邊發(fā)毛
原由:壓力調(diào)節(jié)欠妥或印版溫度太低
處理辦法
1、調(diào)節(jié)壓力,局部墊版;
2、適當(dāng)加強燙金溫度。
故障4:印跡金屬光澤降低
原由:印版溫度過高。
處理辦法
1、降低電熱溫度;
2、減少不必要的停機,縮短停機時間。
故障5:印跡不清,缺筆斷畫
原由:遇到印跡不清楚這類故障時,首要要思慮燙金版自己是不是有缺陷,另一,電化鋁太緊,燙印壓力不均,電化鋁太窄或?qū)Ъ埛较蚱频?span style="color: green;">亦是此類故障的起因。
處理辦法
1、更換印版;
2、降低電化鋁張力;
3、局部墊版,保持燙印壓力一致;
4、改用幅面寬有些的電化鋁;
5、調(diào)節(jié)導(dǎo)紙公司。
故障6:不干膠標(biāo)簽燙金中最容易出現(xiàn)的質(zhì)量問題——薄膜材料和UV油墨表面燙金困難,印跡不清
處理辦法
1、選取專用的、配套的燙金箔,盡可能選擇進(jìn)口材料;
2、守護(hù)好印版,需求印版要平整,表面無污物;
3、薄膜材料應(yīng)先進(jìn)行電暈處理,以加強其表面張力;
4、減小燙金面積,保準(zhǔn)印版的平整性和燙印壓力的均勻;
5、運用硬襯墊材料時,需求襯墊要平整,均勻;
6、經(jīng)過實驗找出燙印壓力、速度、濁度、排廢的最佳協(xié)同。
06貼標(biāo)故障與排除
故障1:在油桶等容器上貼大面積的紙類標(biāo)簽時顯現(xiàn)汽泡
原由:標(biāo)簽的存儲環(huán)境與貼標(biāo)環(huán)境的溫濕度相差太大,引起貼標(biāo)后標(biāo)簽快速吸收水分而形成氣泡;或因為貼標(biāo)物體表面不平整或臟污有水泡,引起貼標(biāo)不牢,顯現(xiàn)氣泡。
處理辦法
1、貼標(biāo)前,先將標(biāo)簽在貼標(biāo)環(huán)境中放安置一段時間,使其與環(huán)境達(dá)到濕度平衡;
2、使貼標(biāo)物體表面保持干燥、潔凈,并在貼標(biāo)時用力貼平,貼牢。
故障2:透明薄膜標(biāo)簽貼在透明瓶體上后了顯現(xiàn)汽泡,影響美觀
原由:瓶體表面不平整,有微小凹坑或標(biāo)簽的軟硬程度與瓶體匹配都將造氣泡;而貼標(biāo)機貼標(biāo)方式與瓶體外形有不匹配或貼標(biāo)辦法不合適,都會使空氣殘留在標(biāo)簽內(nèi),產(chǎn)生氣泡。
處理辦法
1、貼標(biāo)前檢測瓶體是不是平衡,若不平衡,應(yīng)修整生產(chǎn)瓶體的模具。
2、透明專用貼標(biāo)機,用橡膠刮板貼標(biāo)。
3、選擇與瓶體材料相匹配的材料印制瓶貼。
聲明:本文部分內(nèi)容源自網(wǎng)絡(luò),如有侵權(quán),請聯(lián)系刪除
【免責(zé)聲明:本文版權(quán)歸原作者所有,轉(zhuǎn)載僅為傳播更加多信息之目的,并不表率本平臺贊同其觀點和對其真實性負(fù)責(zé),僅供參考!如有疑問,或侵權(quán),請聯(lián)系印務(wù)通博主(ywtswt)】